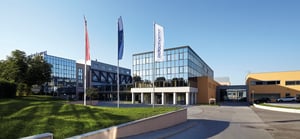
Enhancing Plasma Safety and Compliance through Technology
Octapharma, a global leader in plasma collection

Operating 150+ sites
Octapharma operates over 150 sites dedicated to the development of life-saving plasma products.

195+ donation centres
Octapharma is one of the largest human protein product manufacturers with 195+ plasma donation centres.

11,908 Employees
Octapharma employees thousands of people across 5 state-of-the-art manufacturing sites
The Challenge
The plasma collection process is highly sensitive, requiring precise temperature monitoring to guarantee the safety and efficacy of plasma products. Prior to technological intervention, Octapharma relied on manual monitoring and paper chart recorders, processes fraught with human error, time-consuming report generation, and potential data integrity issues.
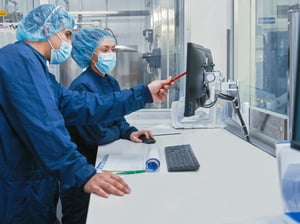
The Solution
To overcome these challenges, Octapharma turned to Checkit. This solution offered an automated, digital alternative to manual monitoring, ensuring accurate, real-time temperature monitoring across all collection sites.
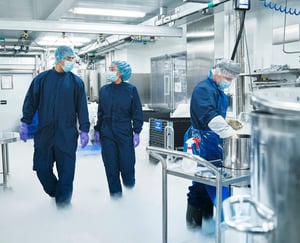
The Implementation
The transition to Checkit system's marked a significant shift from analog to digital, eliminating manual recording errors and streamlining data capture. This change not only improved process efficiency but also ensured complete and reliable temperature monitoring, critical for maintaining plasma integrity.
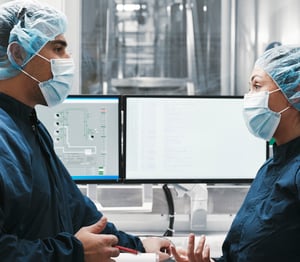
The Benefits
Complete Data Capture: Checkit provided uninterrupted temperature monitoring, ensuring that no readings were missed and all data was accurately recorded.
Automated Reporting: The system facilitated automatic generation of compliance reports, significantly reducing the time and effort involved in manual report creation.
Process Efficiency: The automation of temperature monitoring processes resulted in enhanced operational efficiency, allowing staff to focus on core activities rather than manual data recording.
Exceptional Customer Support: Octapharma highlighted the outstanding customer service provided by Checkit, which was instrumental in the smooth implementation and ongoing operation of the system.
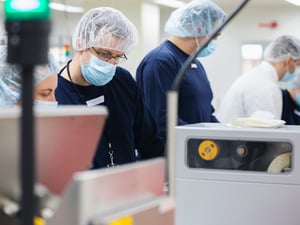
"The plasma industry is a highly regulated industry with strict temperature requirements... When we switched to Checkit, we no longer had issues such as graph overruns, missing data due to tracing issues, and having to manually interpret temperature values... This has resolved all of our temperature tracing problems... The customer service has been outstanding."

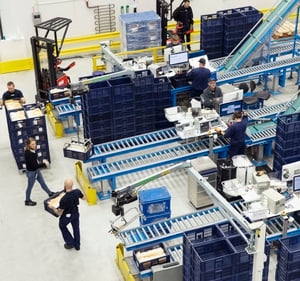
Conclusion
Octapharma's adoption of Checkit illustrates the transformative power of digital solutions in highly regulated and sensitive industries like plasma collection. This case study showcases how technological advancements can significantly enhance compliance, data integrity, and operational efficiency, thereby contributing to the overall safety and efficacy of life-saving plasma products.
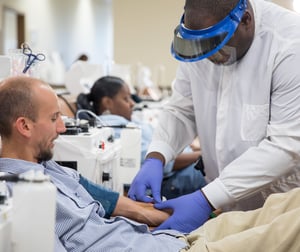