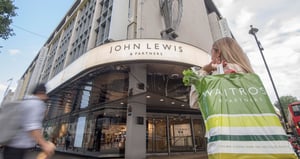
How Checkit Delivers £28m in Value for the John Lewis Partnership
Driving operational innovation across food and home retail use cases

2 premium brands
John Lewis and Waitrose are market leaders in food and home retail

430+ locations
Total sites across all their retail, food, and other customer-facing locations

74 million customers
Total number of customers served weekly by the business partnership
The Challenge
The John Lewis Partnership faced significant operational challenges causing issues with safety, compliance, and the customer experience.
Challenges:
- Rising store energy costs, asset maintenance issues, and stock wastage, was leading to increased operating expenditures.
- Inefficient, time consuming, and expensive safety and compliance processes for thousands of checks.
- Errors, inaccuracies, and rework resulting from manual processes.
As a business, they needed to focus on finding operating and productivity efficiencies without impacting the overall customer experience. They also needed to develop proactive processes that give them increased control and visibility.
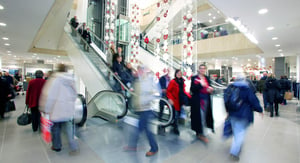
The Solution
John Lewis and Waitrose collaborated with Checkit, transitioning from manual and inefficient procedures to digitized and automated systems.
- Over 22,000 refrigeration assets were selected for advanced sensors, real-time asset monitoring and alarming software, along with comprehensive food safety monitoring services.
- Store maintenance and food service team members were equipped with Checkit digital assistants, designed to prompt, guide, and document their daily activities. This ensured the completion and digital recording of all essential compliance, safety, and maintenance tasks. Through this digital transformation, the teams at John Lewis and Waitrose could streamline their operations, enhancing efficiency and ensuring adherence to safety and compliance standards.
This partnership enabled the monitoring of over 22,000 refrigeration assets around the clock, employing advanced sensors, real-time asset monitoring and alarming software, along with comprehensive food safety monitoring services.
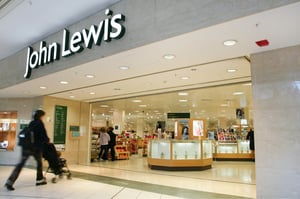
The Results
Using Checkit sensors, software and services, together with web-based dashboards, managers of different levels of seniority across the business have significantly improved control and visibility of major cost variables.
Driven by actionable insight, the Checkit platform delivers more than £28m of annual savings and repurposed staff time:
▶ £24m worth of repurposed staff time
▶ £3.6m of food wastage avoided
▶ £0.8m from optimized energy usage
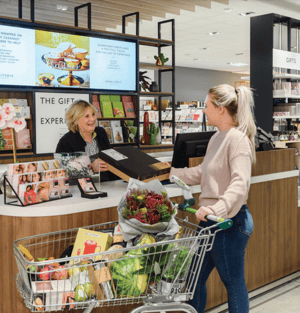
The Expansion
Checkit foresees the opportunity to deliver further tangible business benefit in future, via the expansion of John Lewis’s existing sensor ecosystem and additional workflow automation through new software use cases.
We predict that the efficiencies and actionable insight these potential opportunities can deliver would equate to a further £7m of annual savings.
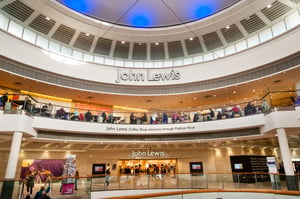
The Results
“With all of the data now being managed digitally by Checkit, we have seen improved efficiencies in our day-to-day operations and compliance activities. We are actively exploring future expansions in how Checkit can further build out our operational ecosystem."
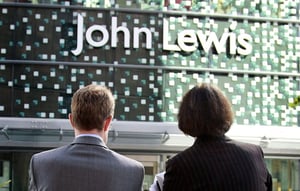
Get in touch to get started
Interested in how an intelligent operations platform like Checkit can improve your operational efficiency?Request a demo with one of our experts to see Checkit in action and find out how it could help your team.